A5: Wizard of Oz Prototyping
PROTOTYPE
For this assignment, we wanted to create the false-reality of a third-party gesture recognition device/software for an Apple TV. To do this, we used a few visuals along with a well-written facilitator script. Our visuals included a Kinect "plugged into" the Apple TV, an infographic hanging from the TV as a reminder for the participant of the various gestures that were available to them, and lastly, a non-instantaneous reaction time with a consistent delay from the user making the gesture to the action being performed by the Apple TV. In reality, the Kinect was doing nothing, and I was actually controlling the Apple TV using the remote under the table that I was "taking notes" at. We ended up having two participants and both were fooled by our usability testing of our "new device".
Owla and I sitting behind where the participant would stand, facing the TV
The TV with the gesture infographic - easily viewable by the participant
The Kinect "connected" to the Apple TV
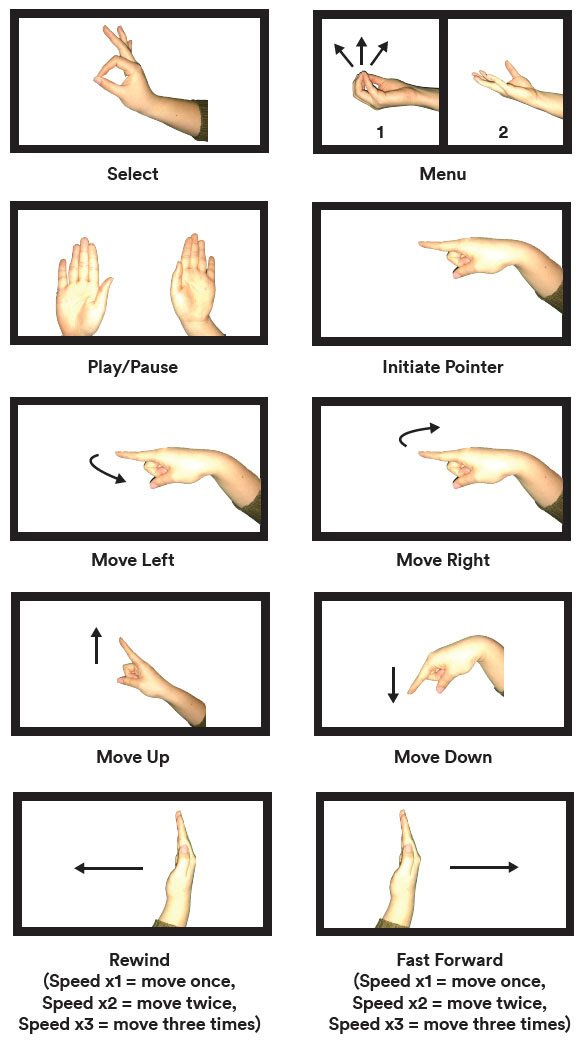
Gestures infographic
ANALYSIS
Overall, the facade we created worked very well. One issue we ran into just before testing our participants was that the remote was loud and could be heard when being clicked. In order to mitigate this and ensure that we didn't break the facade we had created for our participant, we used a sweatshirt wrapped around my hand holding the remote to mute the clicking sound. Luckily, both of our participants were fooled by our prototype and we also got some good feedback. Originally, our video had a fairly big part of the "reveal" included - the part where we informed the participant that what they experienced wasn't real. However, in our in-class critique, we were told that while the reveal is interesting to watch, it isn't as useful in conveying how effective the prototype was as the feedback that we received from the participants. Therefore, after the critique, we edited our video to include participant feedback instead of showing their reaction to discovering the reality of the prototype.
A4: Headspace Video Promotion
DESIGN
In creating my video promotion for the Headspace app, I knew that I wanted to try and create a sense of need in the viewer. While designing how the promotion would flow, I wanted to try and create this sense of need by having very little narration and having the visuals and audio in the promotion communicate the effectiveness of the product. Seeing as how my target audience for this was college students, I made the assumption that canvas would be a well known tool. In the video, the subject is visibly stressed and anxious about having multiple assignments due the same day. After using the Headspace app, the subject is able to organize their thoughts and complete everything on their “to-do” list.
STORYBOARD
To start designing the video promotion, I created a storyboard with what I imagined the video looking like. After creating the storyboard, I got to shooting the video based on the storyboard. Some adjustments had to be made to fit within the time constraint and to make the video more clearly convey what I intended.
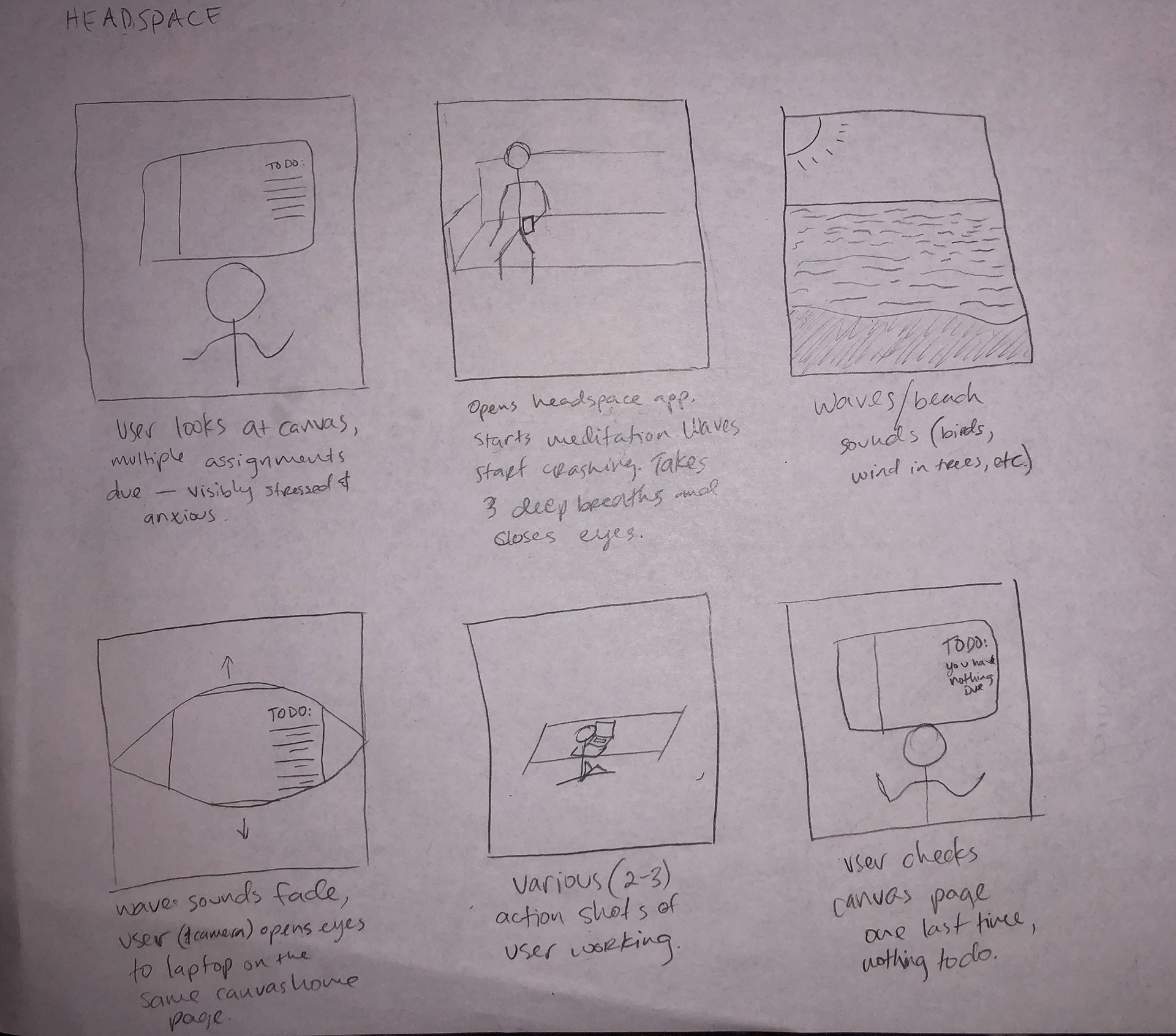
ANALYSIS
In the critique of my video promotion, I gained two meaningful insights from viewers. First, the general message is effectively conveyed - the viewers understood that the meditation helped the subject reduce their anxiety and stress, allowing them to complete their tasks. Second, not having narration doesn't necessarily hurt the video, but it could make it more clear, especially for portion where the subject uses the app. However, my largest takeaway from creating a video promotion is that you need to make sure to have all of your footage perfect the first time around to keep that feeling of a continuous shot. After receiving my critique feedback, I wanted to go back and shoot a scene of the app being used to convey that portion of the promotion a little more clearly. Unfortunately, I no longer have access to the space where I shot the original footage and the date would be different on my computer which would make it very difficult to keep that continuous shot feeling. Since that would require far too much effort for the scope of this assignment, I decided to just add a few small narrations to give the video that extra little bit of context.
A3: 3D Printed Object
DESIGN
This object was designed in Rhino using a variety of features. Initially it started with a single outline of the object from the side which was then revolved 360º to create the pot. The text was created, molded to the shape of the pot, and then cut out from the design and lastly the base on the inside was filleted for a smooth, round bottom edge to make cleaning the pot easier if needed.
REFLECTION
Designing this object was very fun. Initially, I wanted to design a cookie cutter but quickly realized that the cut-out I had started to design (which was quite intricate) had walls that were too thin to last for multiple uses and would be far too difficult to fix within the time constraint. This is definitely something I wish I had thought about sooner as it took up a good amount of my time before I realized. I switched directions and designed a pot instead because I had a plant that needed a home. Theming it after Winnie the Pooh's "Hunny Pot" I got to designing in Rhino. The software has a lot of finite control which can be helpful at times but also make it difficult to work with. Specifically, the FilletEdge command was very difficult to work with. On basic shapes it is quite intuitive and easily rounds corners – a very useful command to use. Unfortunately when I attempted to use it on the script font I was using for the text, it had a lot of major issues which basically would destroy my design. The finite control gave me some hope as I played around with the small handles that control the level of filleting in specific areas since it made the problems slightly better at times, but ultimately I could not make it work and just left it alone. Since there was a snow-day and we had extra time before the critique, I decided to paint the pot and fill it with the plant. This design took me quite a bit of time, but the overall experience I had throughout the process was good.
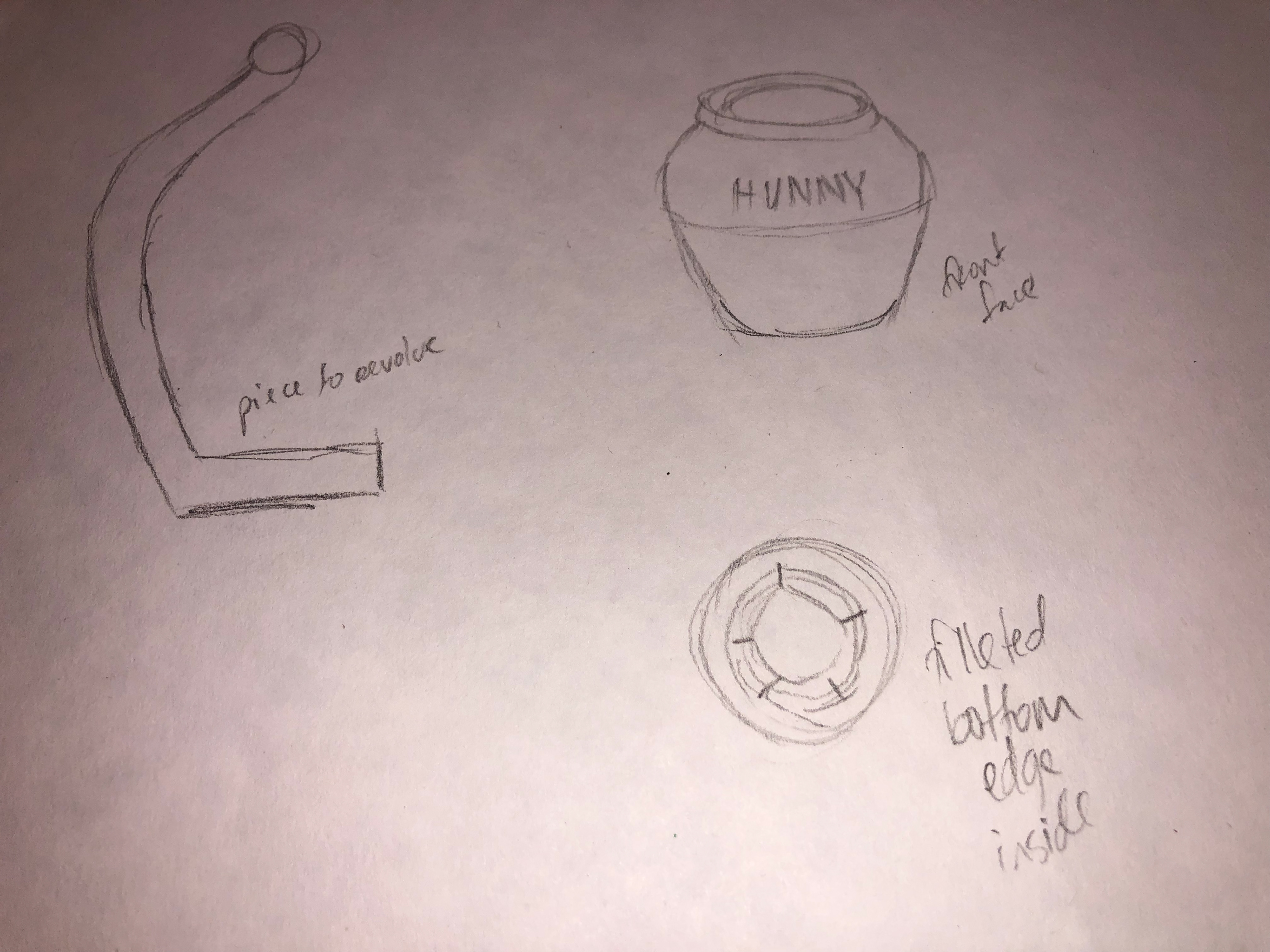
Initial sketches of the design
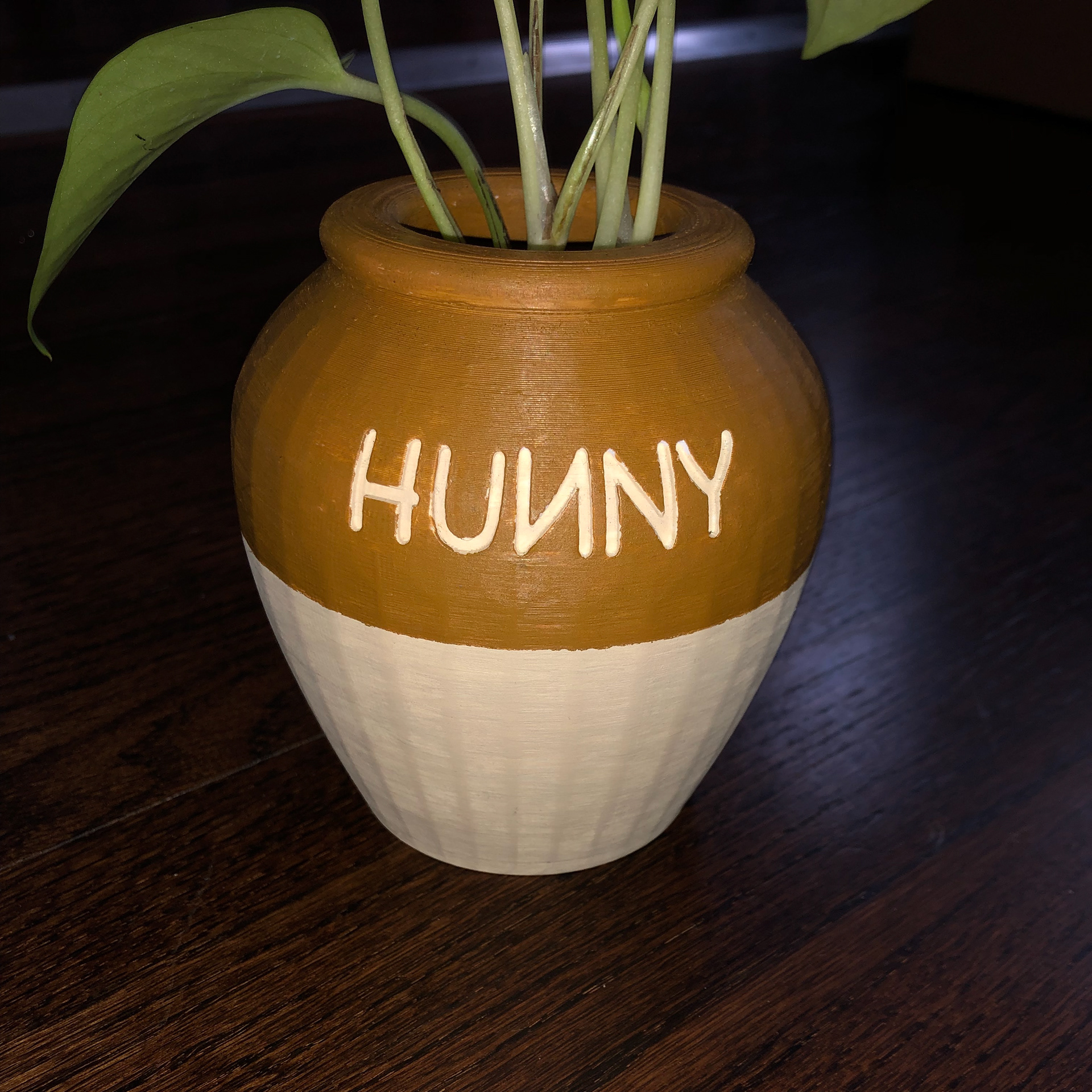
A closeup of the prototype
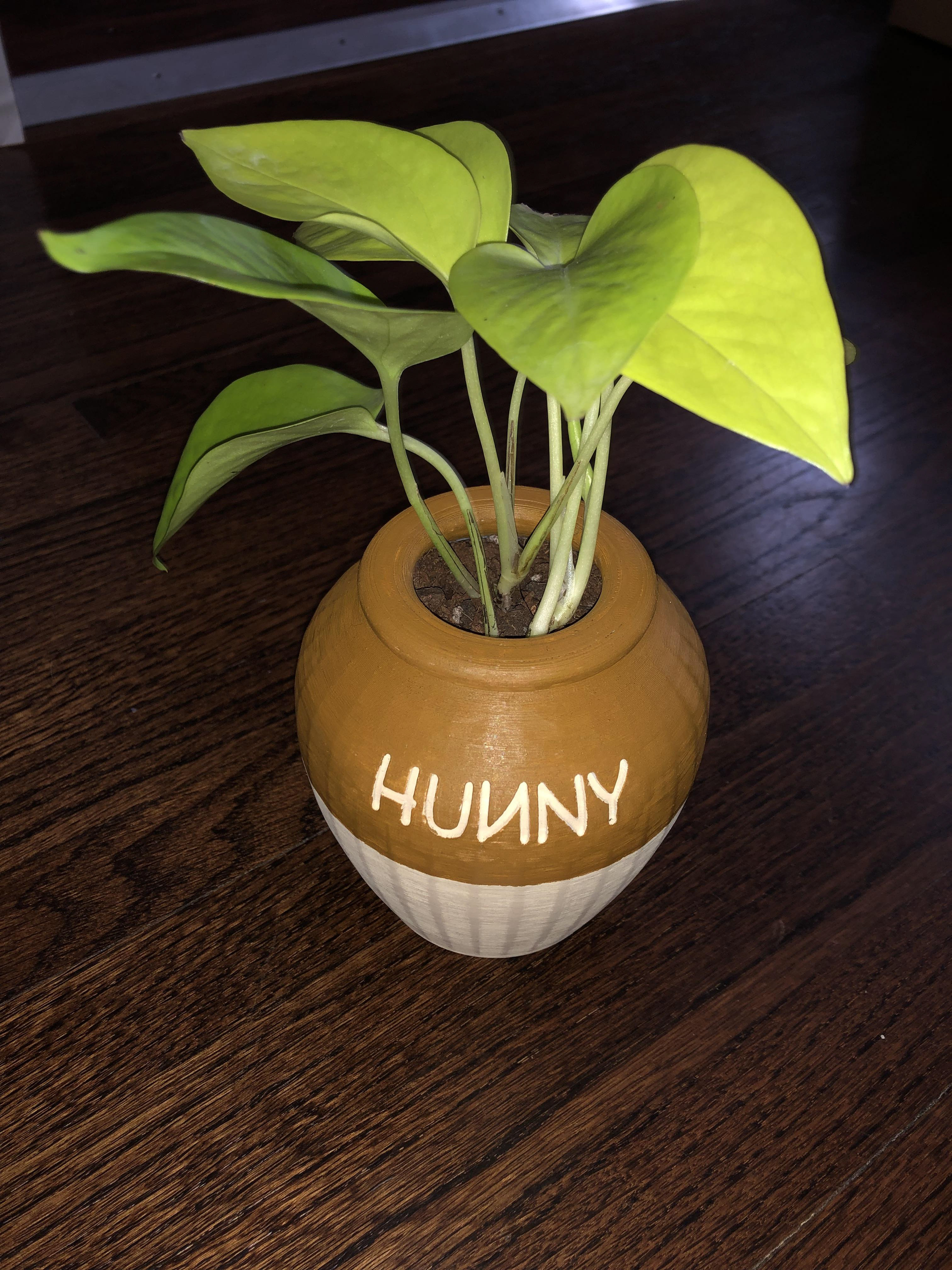
The finished product
A2: Laser Cut Object
DESIGN
This design consisted of a single sheet of .022" chipboard (or matboard) with the constraints that we could only use one sheet of the material, could not use any tape or other adhesives, and that the design must be able to flatten completely for transportation or storage purposes.
For images of my design, please see below.
ANALYSIS
Working on this project, I think the number one thing I learned is that you really have to think through every aspect of your design before printing if you want to only print once. While the overall idea of my design worked well from the start, a lot of small things needed addressing which I hadn't fully thought through in my sketches and initial design. The one aspect of the design that was most difficult to get correct was what type of mechanical lock to use in order to keep the front face of the stand held up with enough strength to support the phone, and also have it be easy to setup. I considered using a second piece on each side to lock the front face of the stand to the sides of the stand, but my goal with this design was to have one single piece that makes up the stand. By keeping the design one single piece, the user doesn't have to worry about losing anything which would make the product no longer functional. I think in the end my design worked quite well. The pros include very quick setup (around 30 seconds), a sturdy design that won't easily collapse, and very low profile storage. The cons are that the sizing of the stand is slightly off due to the camera placement and the camera cutout is barely (and I mean barely) seen through the viewfinder. For a low fidelity prototype, this was a great start.
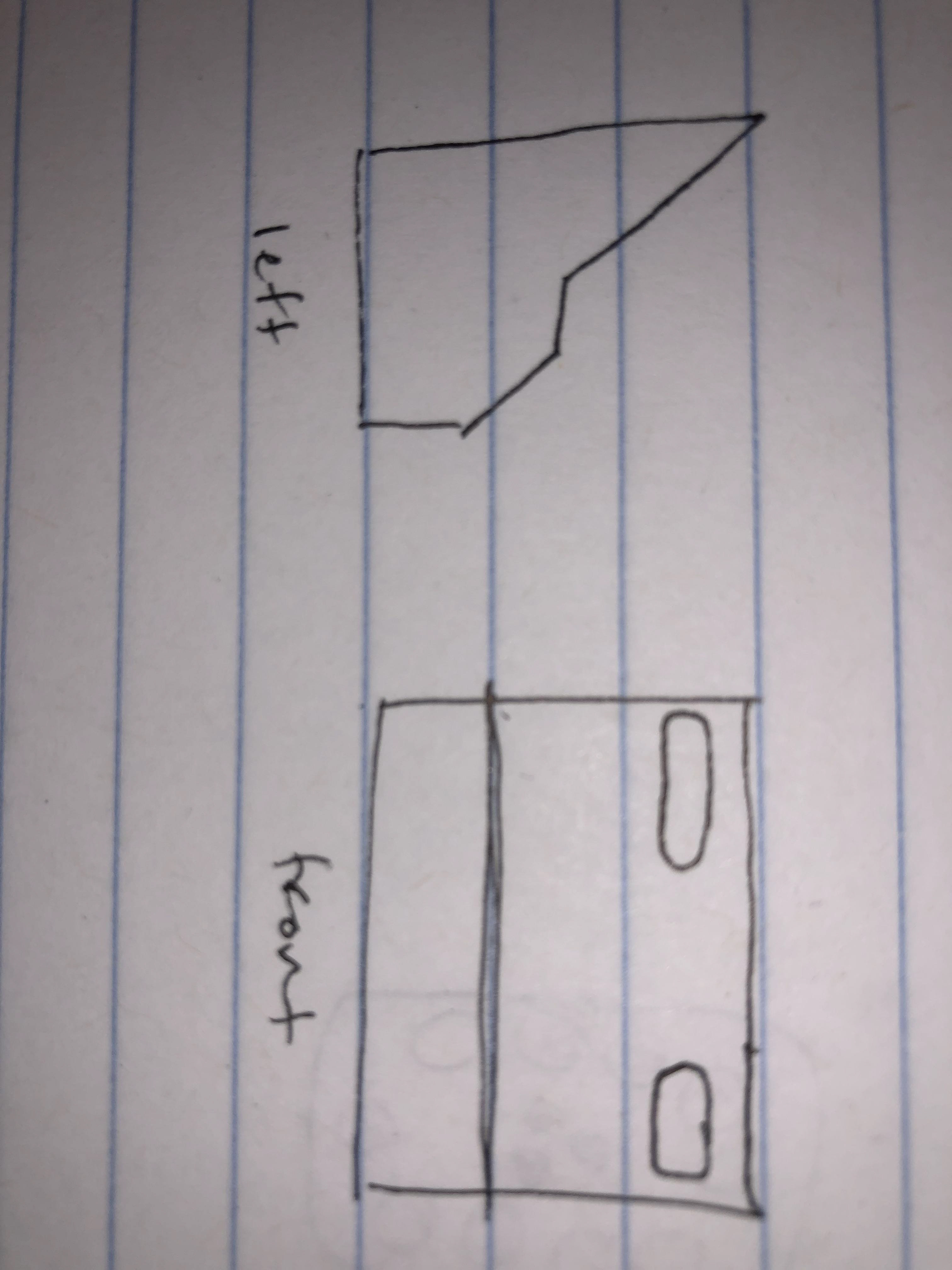
Preliminary sketch for how it could look
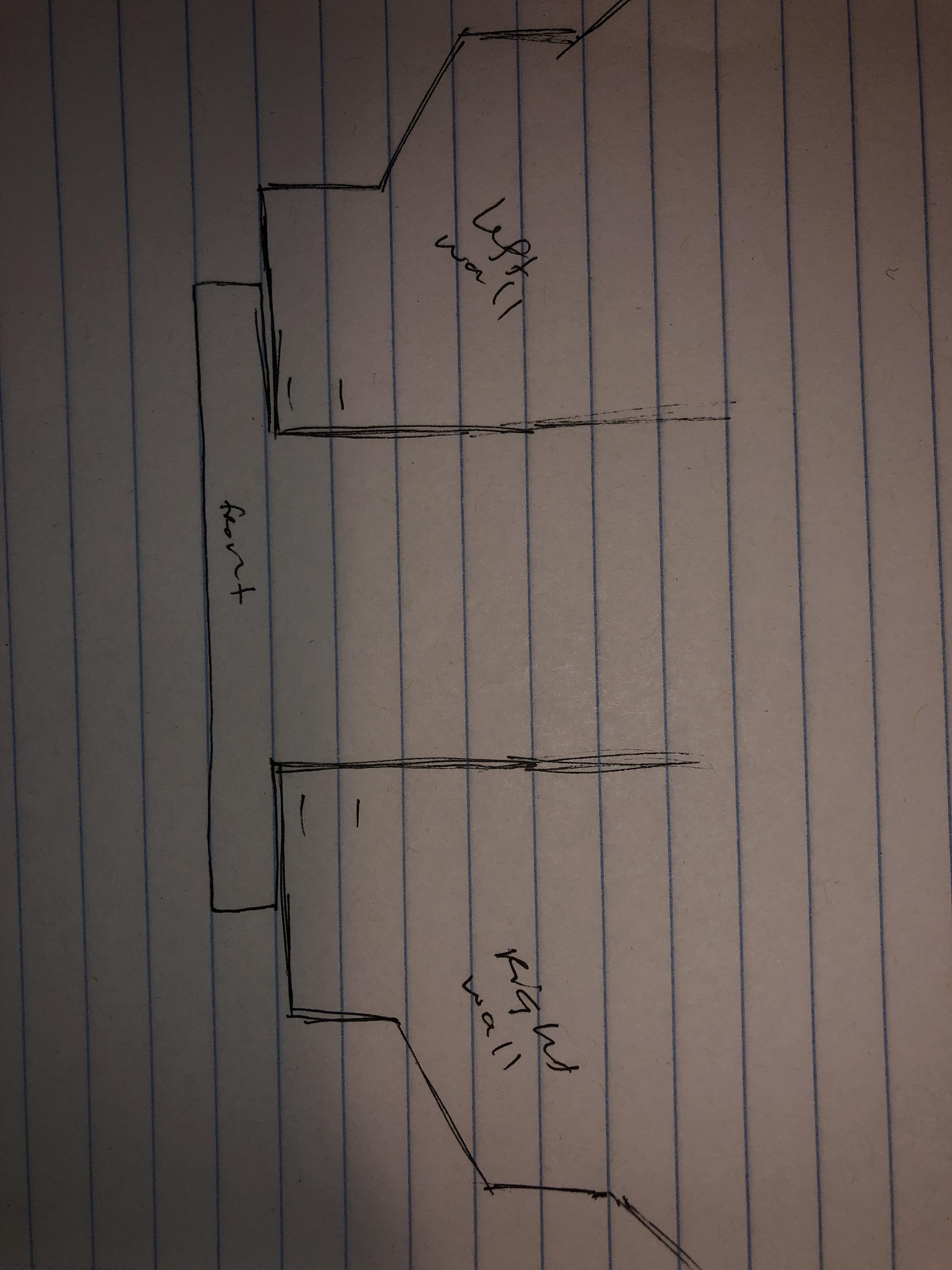
Flattened sketch based on preliminary sketch
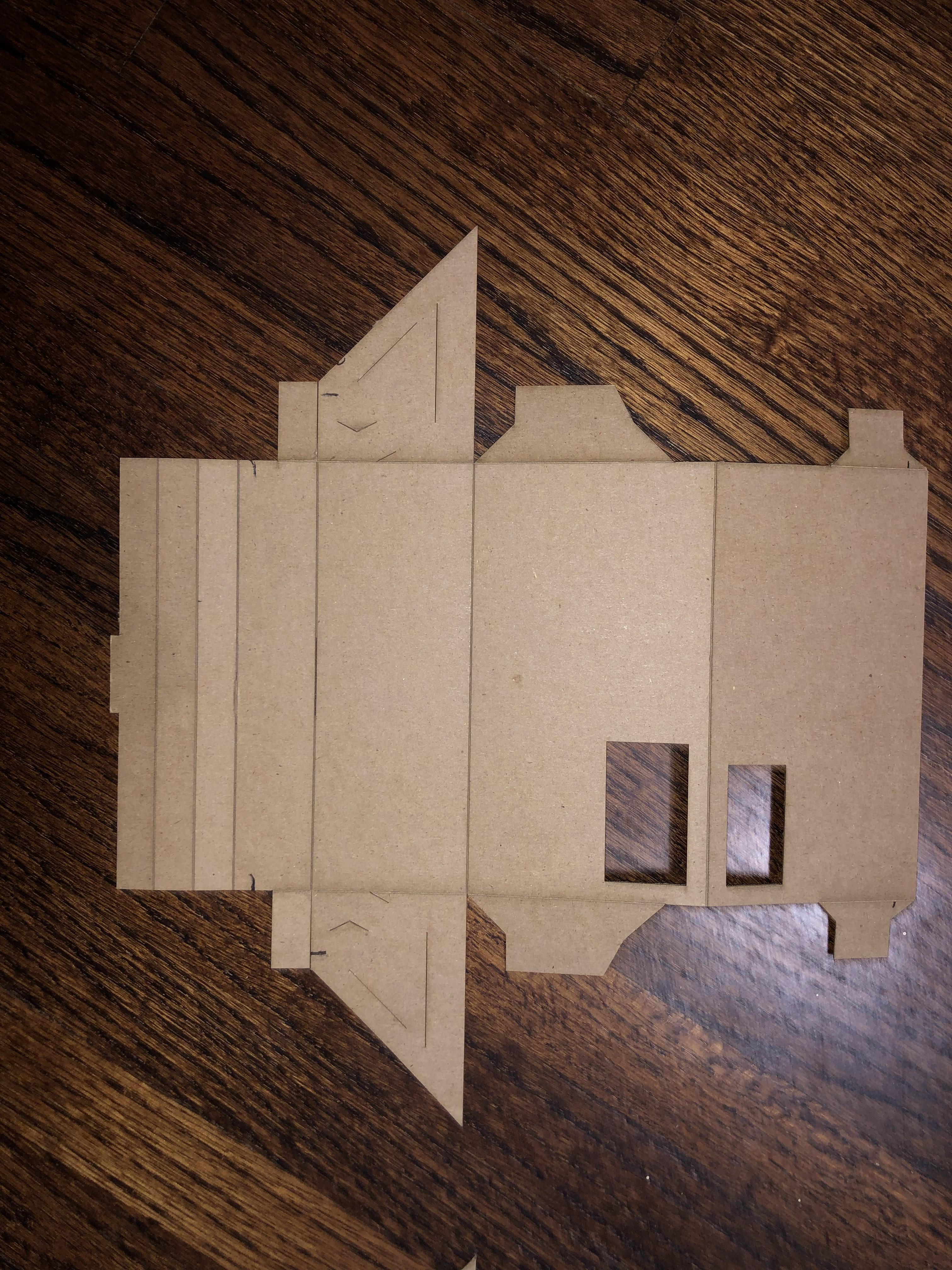
Original design - impossible to close front face without damaging the prototype
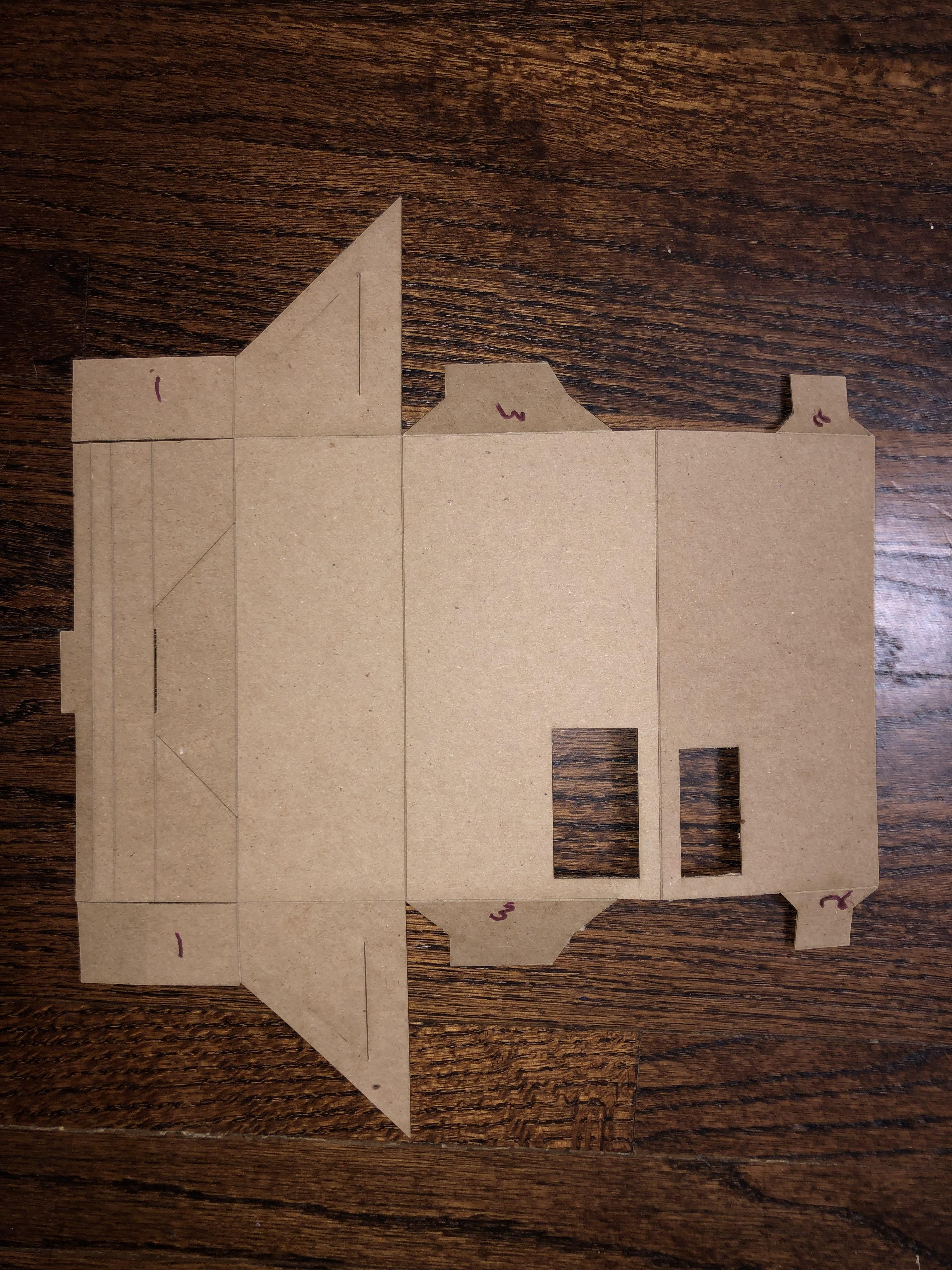
Revised design - fixed front face mechanical lock
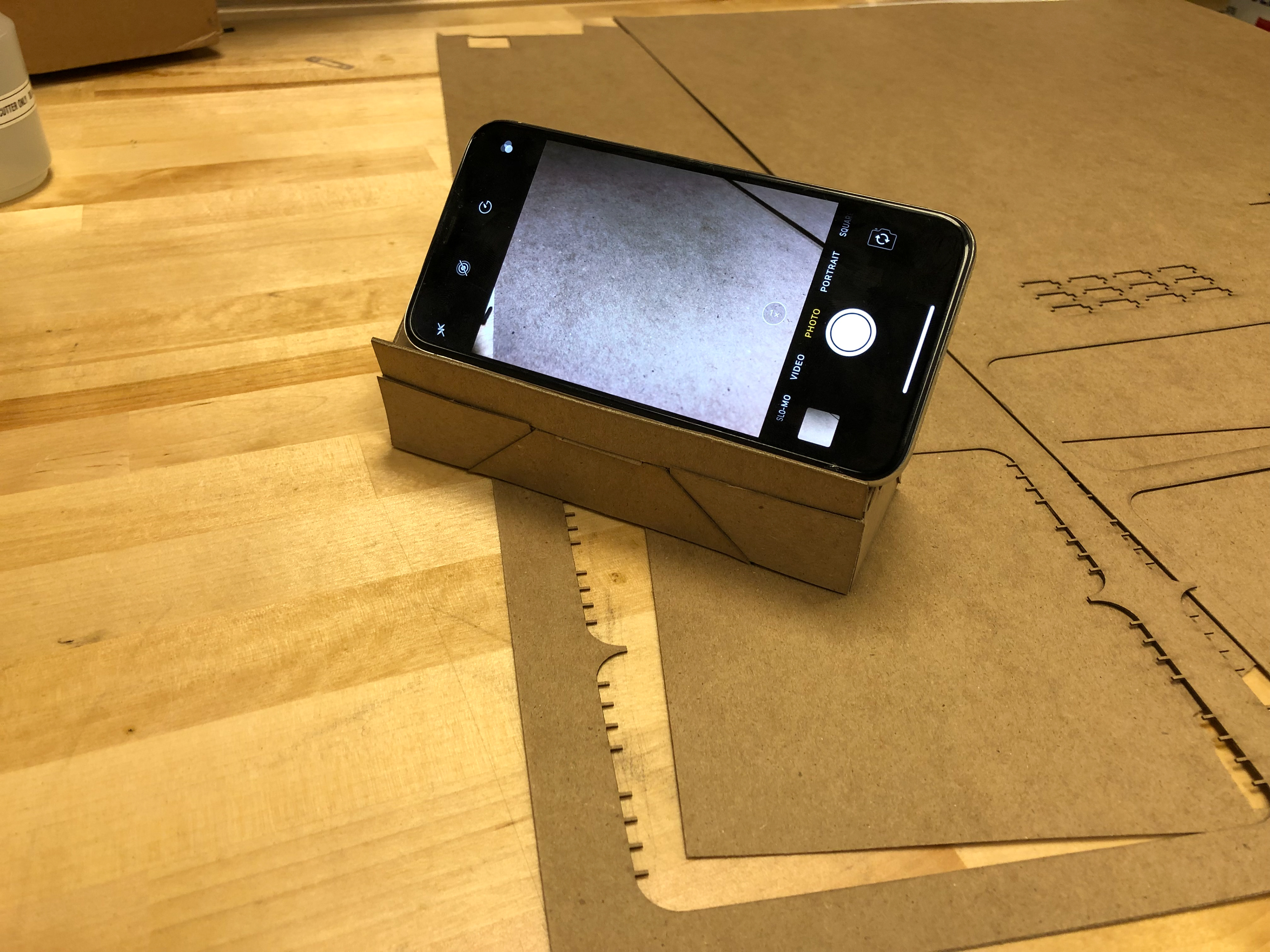
Front view of the prototype with an iPhone X being tested
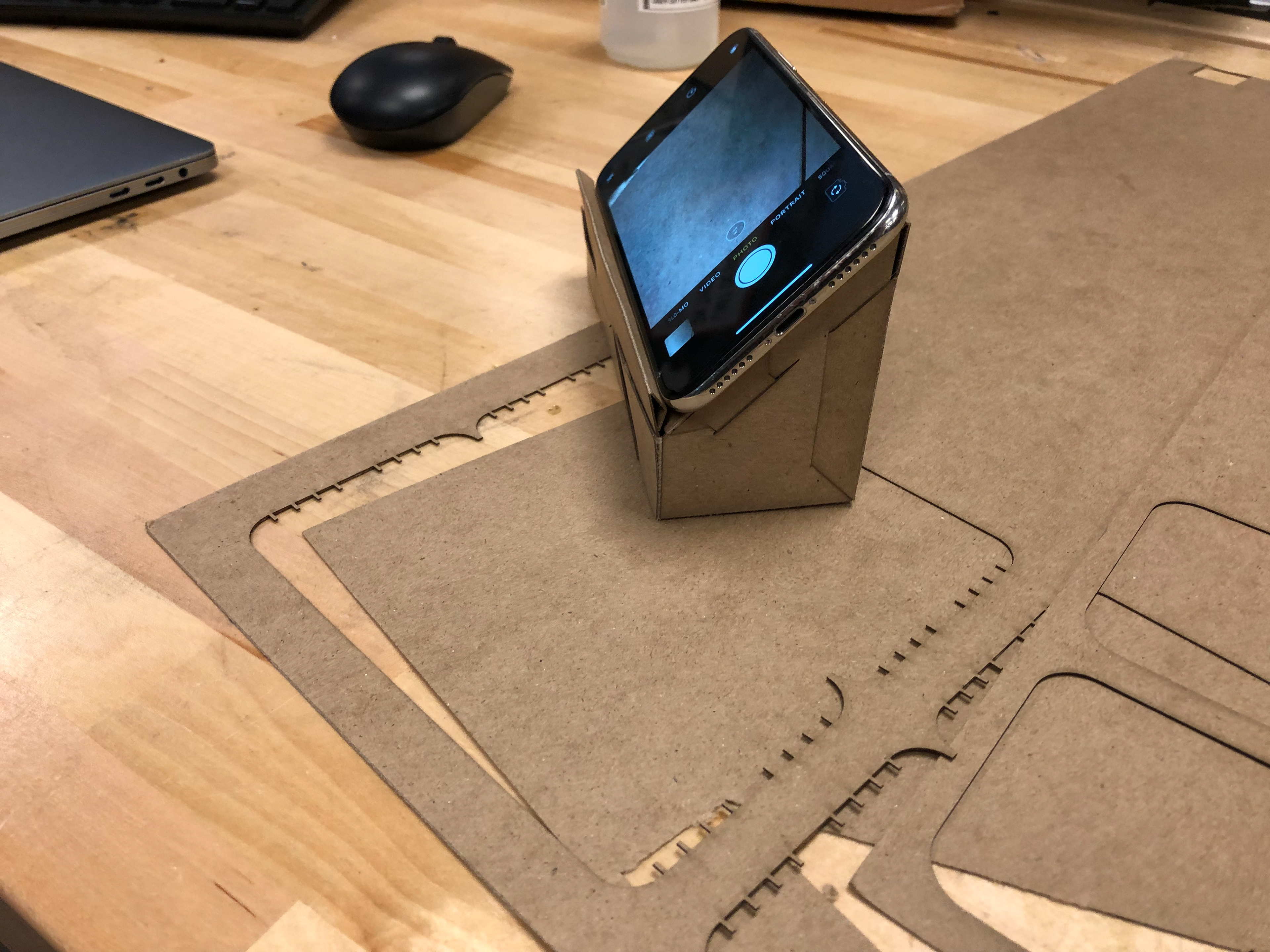
Side view of the prototype with an iPhone X being tested
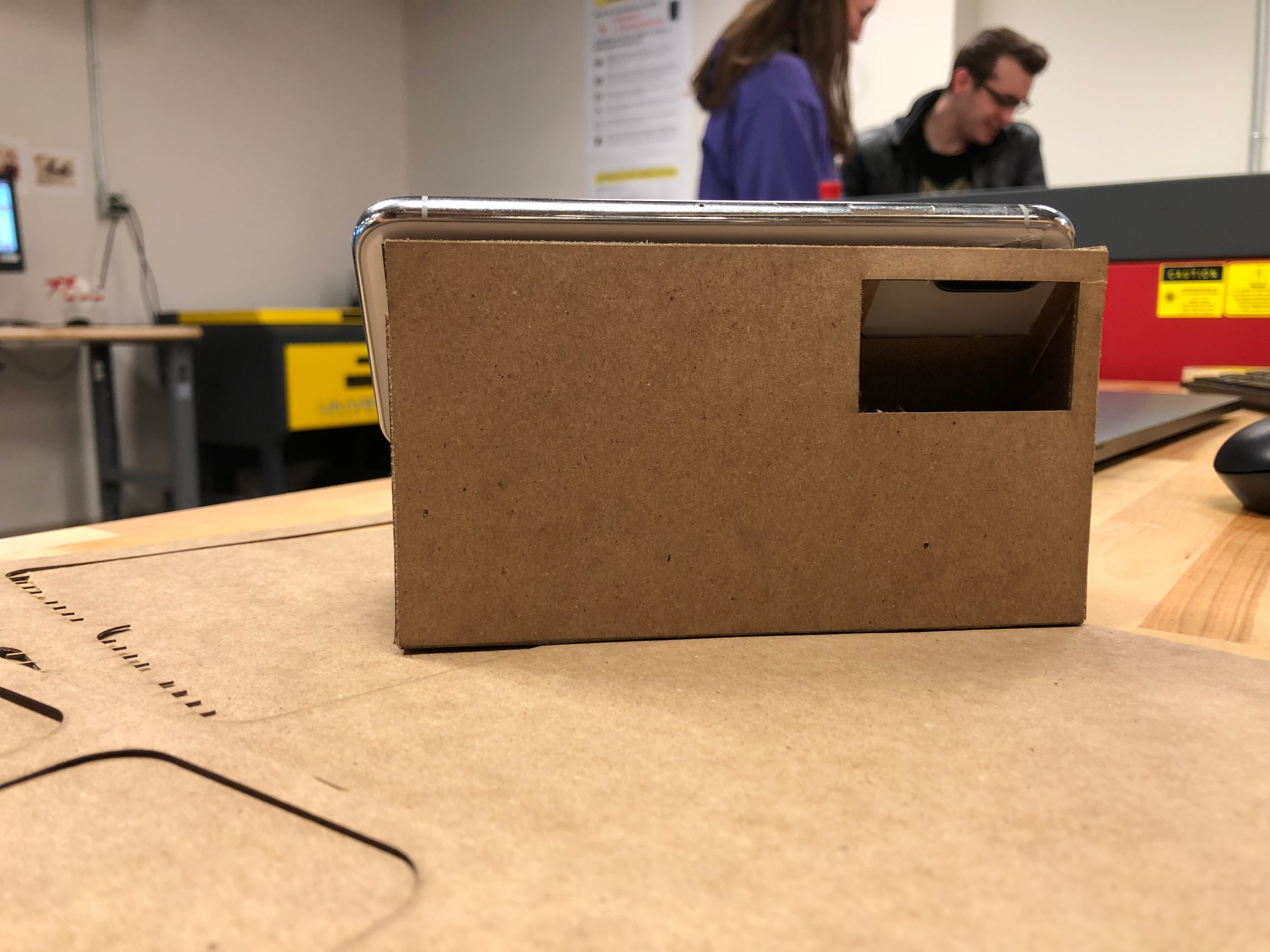
Rear view of the prototype with an iPhone X being tested
A1: Model Prototype
DESIGN
While thinking of how to design this prototype, I knew that I wanted to use OXO's simplistic and "easy-to-use" design style in my own design of this screwdriver. I tried to keep buttons very simple and made sure that a single button does not do multiple things. I also tried to make the form of the product comfortable to hold while performing a task. (Unfortunately this last aspect of the design wasn't entirely fine-tune-able because my plan of "carving" the cardboard after it was glued together didn't work out very well.)
PROTOTYPE
The prototype I created was made from stacked cardboard, has two spring-loaded buttons for engaging the motor in either direction and controlling the speed(this is what I focused on the most in my design/prototype), and ten buttons for selecting the size and type of bit needed.
ANALYSIS
In doing my testing of my prototype, I received mixed feedback about whether my concept of controlling speed with how hard one of the spring loaded buttons was pushed was intuitive and or effective. People either immediately understood the concept without any prompting or people thought something was missing from the design. The ten buttons for size and type of bit worked well, but being a low-fidelity prototype there was at times confusion about whether the buttons should just be tapped or if more needed to be done.
I concluded that the spring loaded buttons was effective since everyone liked the idea after they understood the concept and a lot of the concerns were about intuitive-ness. I think that the 10 buttons however were a little too much. I think a rotating selector switch for both size and type would be more effective than the current setup.
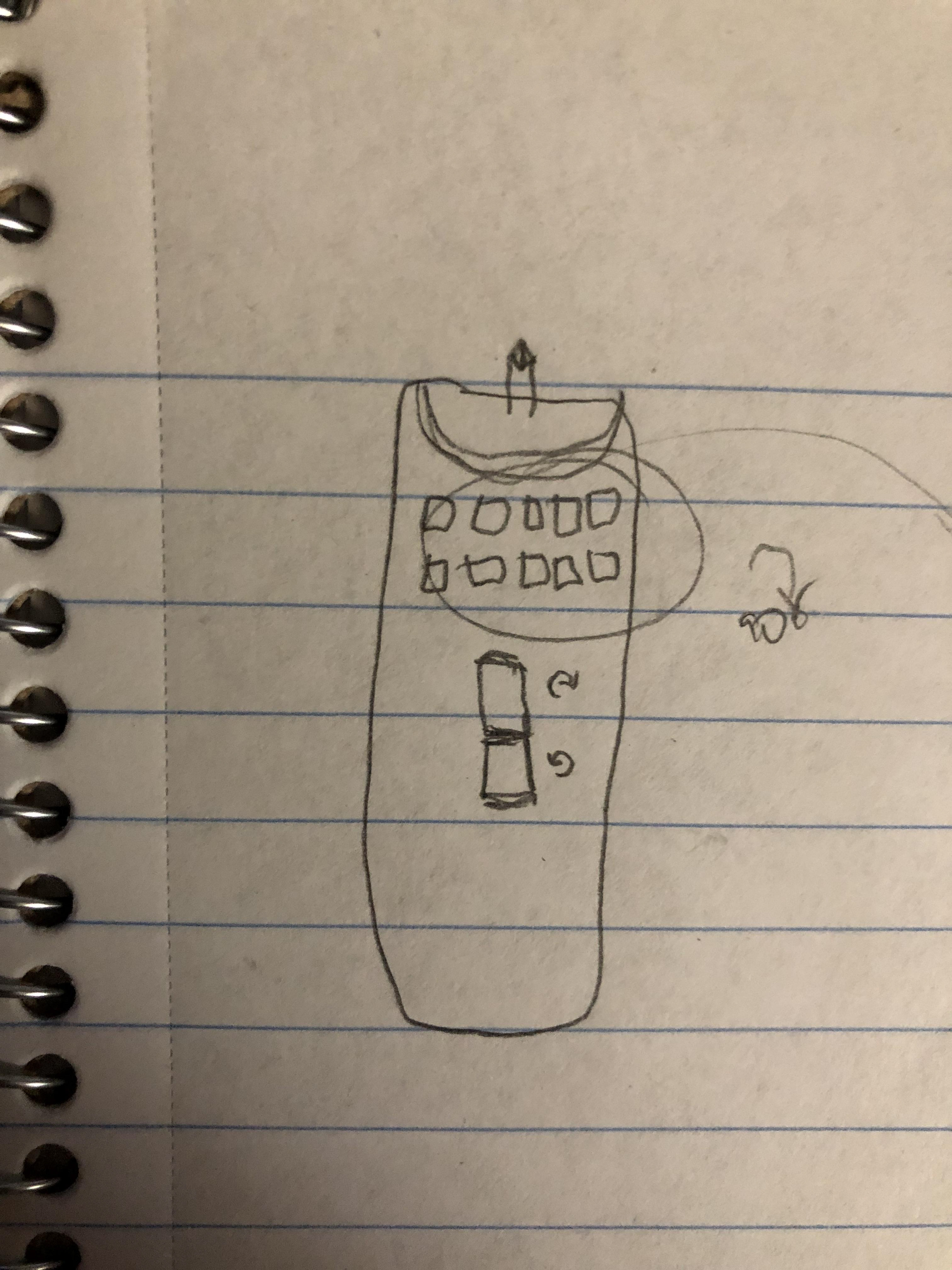
Sketch 1
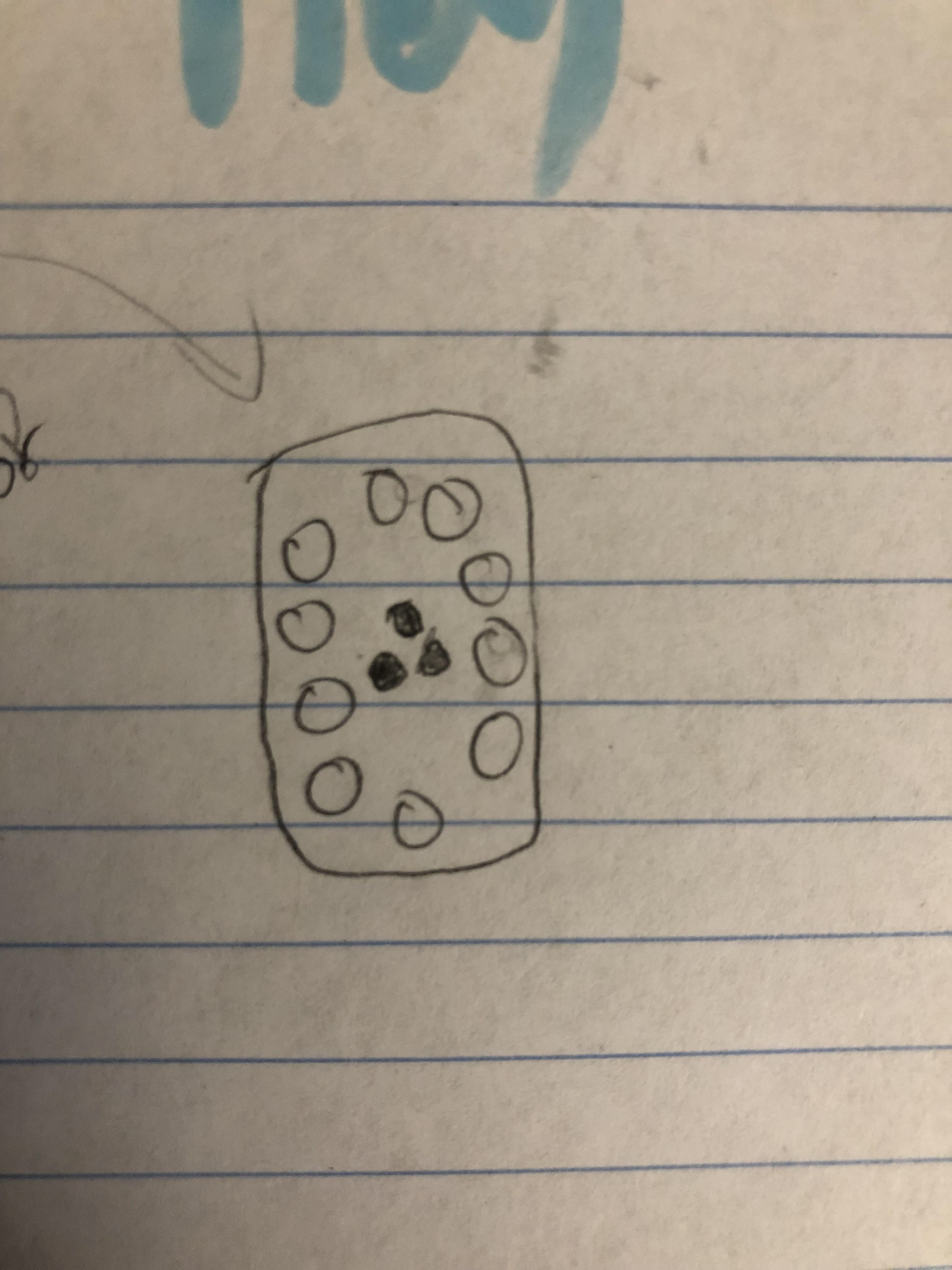
Sketch 2
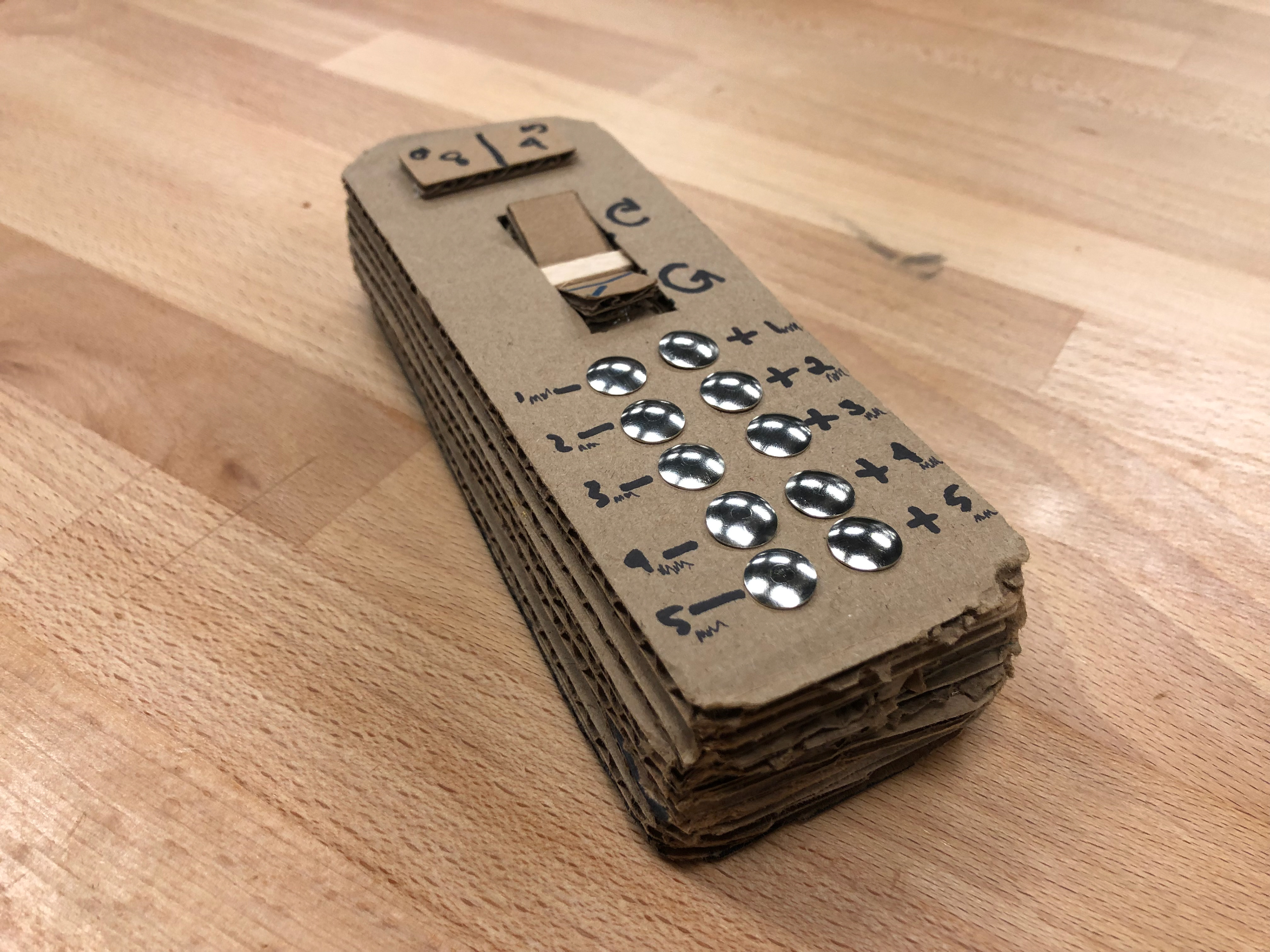
Birdseye
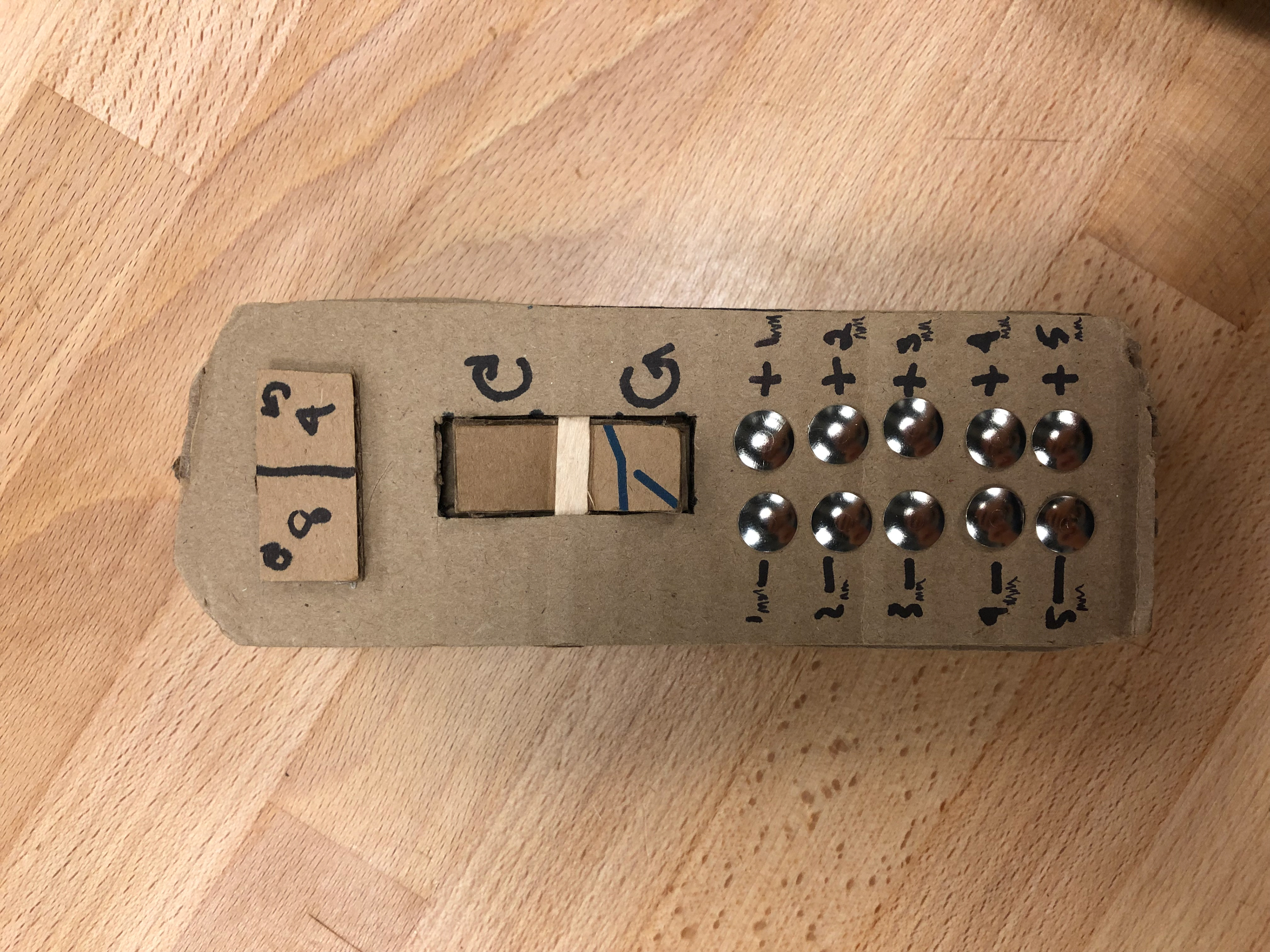
Overhead
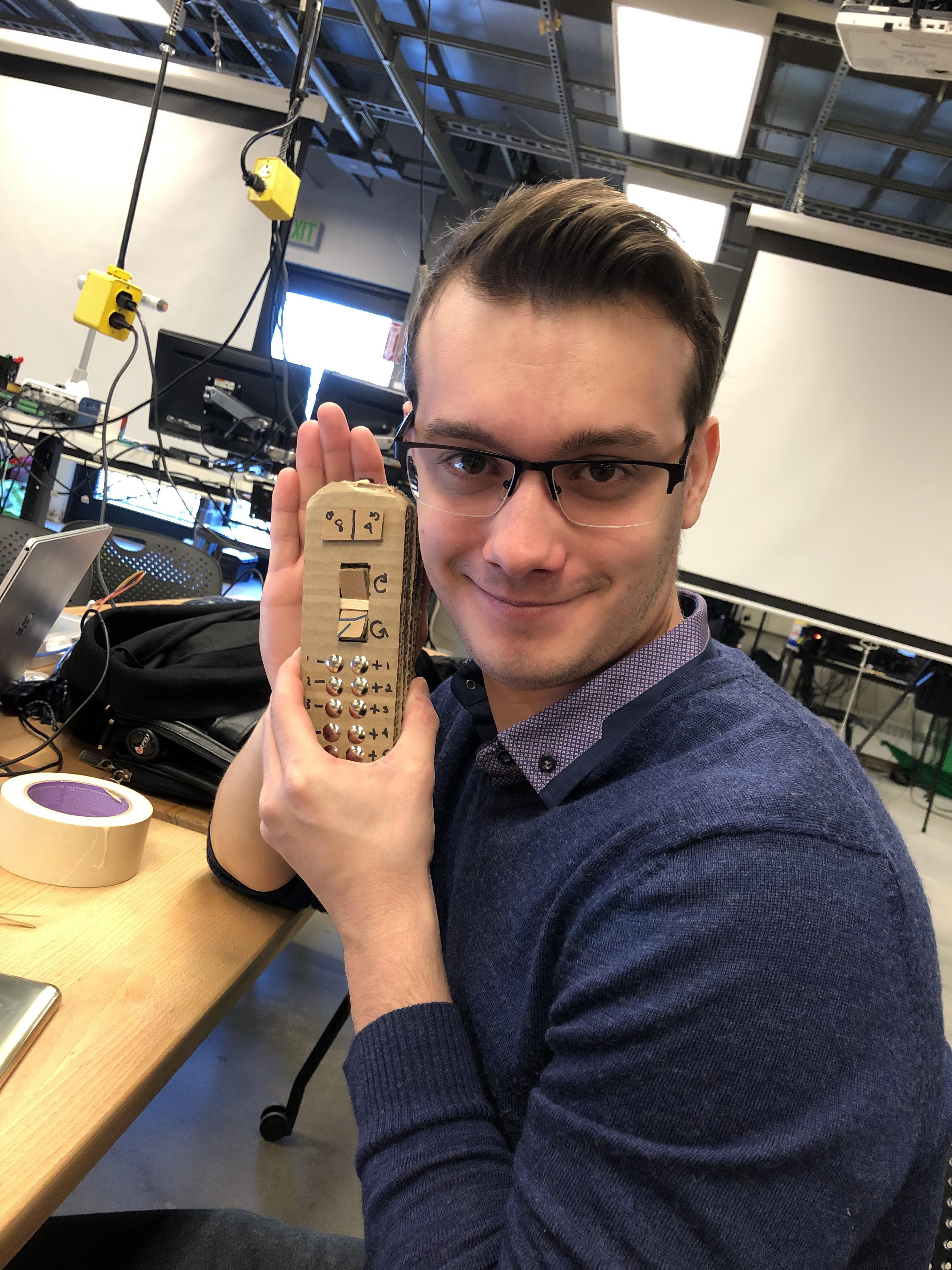
Nikita displaying prototype
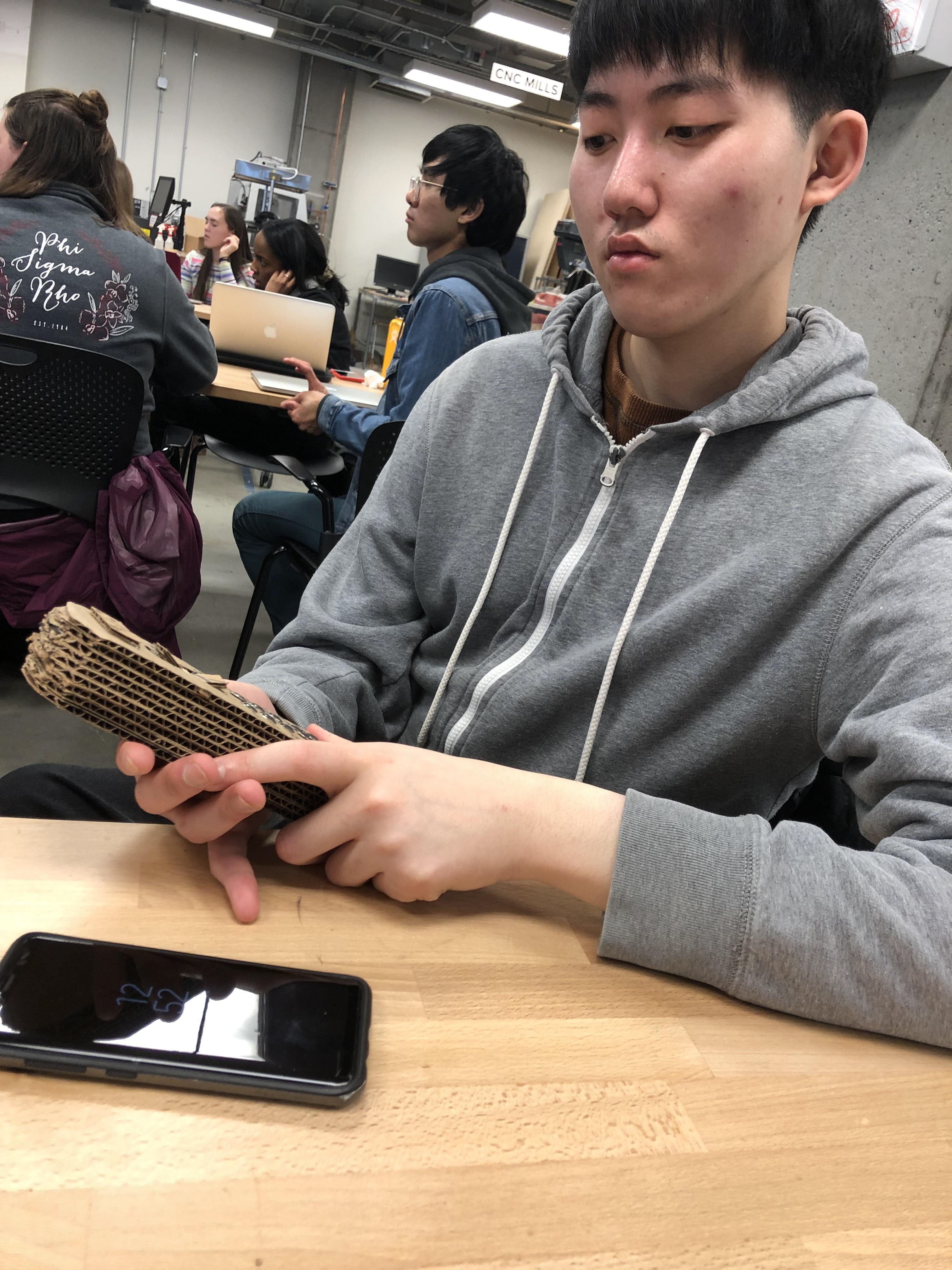
Jang testing
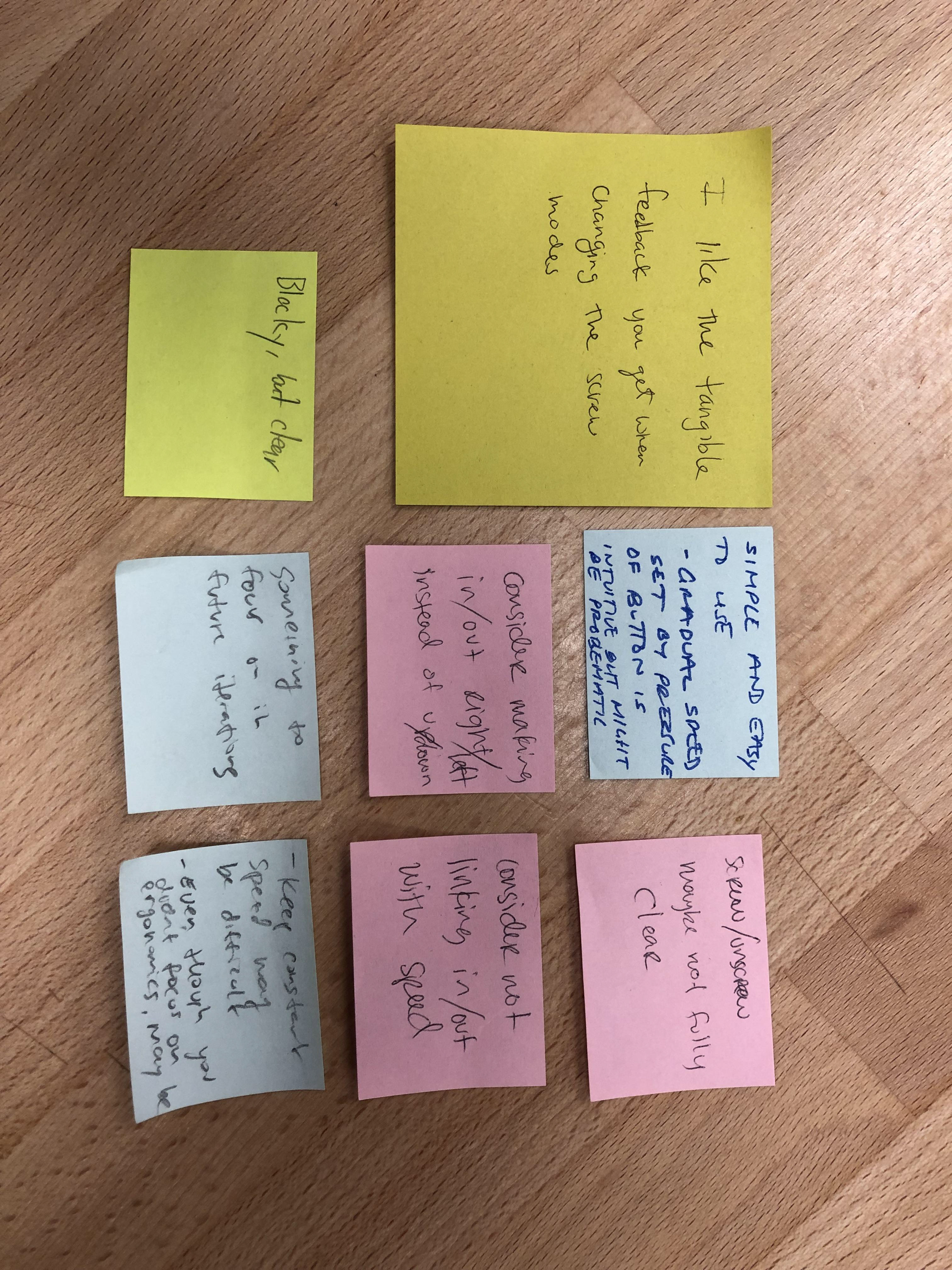